Choosing the right casting service is critical for transforming ideas into high-quality components with efficiency and speed. By offering specialized techniques for various materials and applications, casting services are integral to the production of everything from custom jewelry to industrial parts. In this comprehensive guide, we’ll explore the pivotal role of casting services in manufacturing, helping you pinpoint the provider that aligns with your project specifications and quality expectations.
- Key Takeaways
- Exploring the World of Jewelry Casting
- The Combined Experience of Casting Specialists
- Comprehensive Casting Services for Your Business
- How Casting Creates Value for Clients
- Choosing the Right Casting Service Provider
- Tailored Solutions for Specialized Casting Needs
- Summary
1 KEY TAKEAWAYS
-
Jewelry casting is a meticulous process used to create intricate designs, and professional casting services are sought after by designers for their expertise in metals and precision.
-
Casting professionals contribute valuable experience in creating high-quality products, stay updated with industry advancements, and provide comprehensive services across various industries such as automotive, aerospace, and medical.
-
Selecting the right casting service provider involves considering their experience, capabilities, certifications, and ability to streamline vendor relationships, enhance in-house metal expertise, and offer integrated capabilities like in-house machining.
2 EXPLORING THE WORLD OF JEWELRY CASTING
Jewelry casting is a fascinating process that shapes precious metals like gold, silver, and platinum into intricate pieces of jewelry. This method allows for the creation of detailed elements in:
-
rings
-
watches
-
bracelets
-
pendants
The use of wax, fire, and molten metal enables the production of detailed designs and sculptures that can feature very fine details.
For designers, this foundational service helps to create a tangible object from a concept, providing customers with the opportunity to acquire unique and custom-made pieces.
The Basics of Jewelry Casting
The initial stage of jewelry casting involves:
-
Crafting a wax pattern of the desired piece.
-
Creating a wax mold based on the pattern, which defines the final shape of the cast jewelry item.
-
Filling the mold with molten metal.
-
Allowing the metal to cool and solidify, forming into the shape of the intended jewelry piece.
Part of this preparation involves attaching sprues and a base to the wax model.
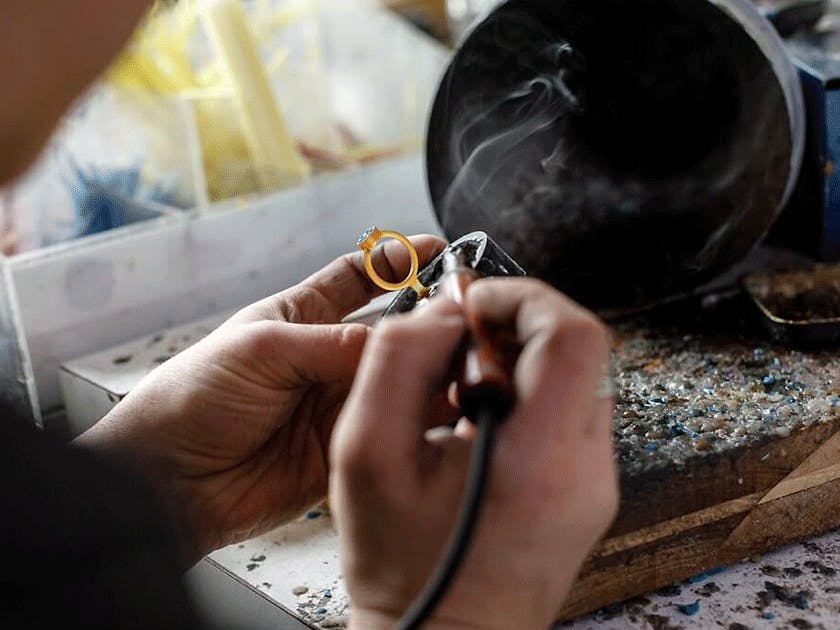
Jewelry Casting by Merrell Casting
From Design to Reality: The Casting Process
The journey from design to reality begins with creating a detailed mold that will shape the jewelry piece. A wax model replicating the final design is formed as the basis of the mold for casting the metal. The molten metal is poured into the plaster mold using a vacuum or centrifugal casting machine.
Upon cooling, the metal takes the shape of the original wax model.
Why Jewelry Designers Choose Professional Casting Services
Professional casting services attract jewelry designers due to the wide range of expertise in metals and casting techniques they offer. These services come equipped with profound knowledge and distinct skills, crucial for custom casting projects. Their expertise includes:
-
Understanding the nuances of metal properties and behaviors during the casting process
-
Ensuring high-quality and precise casting results
-
Providing guidance and advice on design and material selection
-
Offering a variety of casting options, such as lost-wax casting or centrifugal casting
This level of expertise is a significant reason why designers opt for professional casting services.
Designers value the precision casting skills that allow them to reproduce intricate designs without sacrificing detail.
3 THE COMBINED EXPERIENCE OF CASTING SPECIALISTS
Experienced casting professionals significantly contribute to both the quality of the final product and the overall service experience. These specialists acquire valuable knowledge and skills over the years, which contribute to their expertise in producing high-quality pieces. They leverage their experience to develop innovative casting solutions, enhancing service offerings and creative problem-solving.
Their broad range of experience in various casting techniques gives them a versatile approach to different projects.
Expertise You Can Trust
The extensive experience of casting specialists, often spanning multiple years, directly contributes to superior service for clients. This extensive experience not only assures reliability but also strengthens clients’ trust in their comprehensive capabilities.
Keeping Up with Industry Advancements
Casting professionals are committed to staying at the forefront of technological advancements to deliver state-of-the-art solutions. They engage in regular training, are part of professional networks, and frequently attend industry conferences to learn about emerging technologies. Their adoption of technologies such as 3D printed casts offer tailored fit and improved features like lightweight design and enhanced ventilation.
Continual education and adaptation to novel casting techniques play a key role in maintaining a competitive edge in the industry.
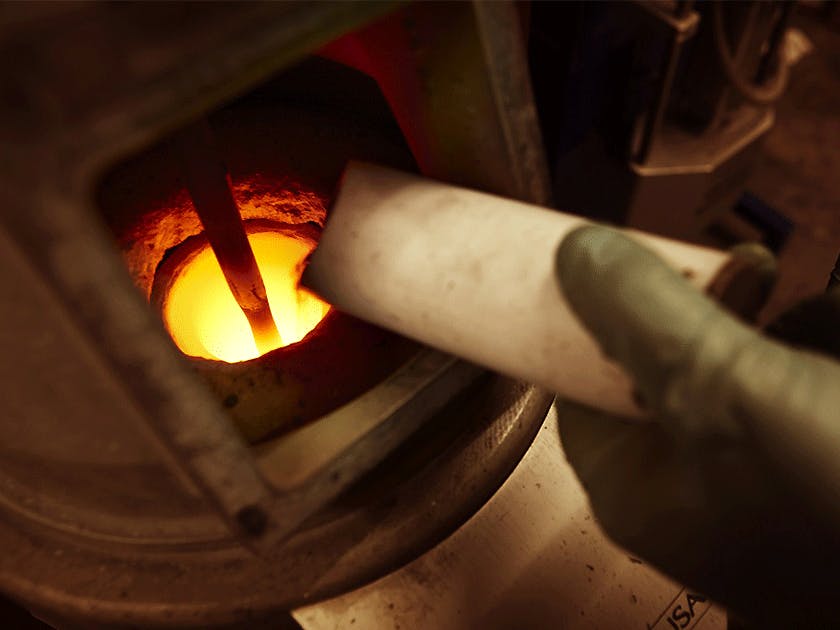
4 COMPREHENSIVE CASTING SERVICES FOR YOUR BUSINESS
Casting companies offer diverse services such as precision zinc die castings, sand and permanent mold aluminum castings, and die castings in aluminum, zinc, and magnesium alloys. Businesses from various industries, including appliance, automotive, construction, medical, aerospace, and consumer products, can access and benefit from these services.
Compared to other production methods, casting services can simultaneously manage multiple development steps, resulting in faster production of castings. To ensure that products consistently meet high standards, casting services implement strict quality assurance and control practices.
Custom Mold Making and Design
Businesses can leverage custom mold-making services, which are vital for the creation of unique product designs. Some casting companies provide special expertise in custom mold making, including tooling design and fabrication, to produce precise molds for their clients’ unique requirements. These specialized providers use materials such as steel and aluminum in custom molds to ensure accuracy and durability in high-volume production settings.
Personalized mold-making services empower businesses to manufacture products that are distinct and tailored to their specific needs.
Investment Casting and Fabrication
Investment casting involves creating a wax mold that is encased with plaster; after baking in an oven, the wax melts away leaving a hardened plaster mold. High-precision parts result from the use of advanced technology and certified processes in investment casting services.
High-precision parts produced via investment casting typically have the following characteristics:
-
Smooth finish that minimizes the need for additional machining
-
Durable metal or epoxy molds, accommodating a range of metal alloys
-
Ideal for long-term use in full production runs
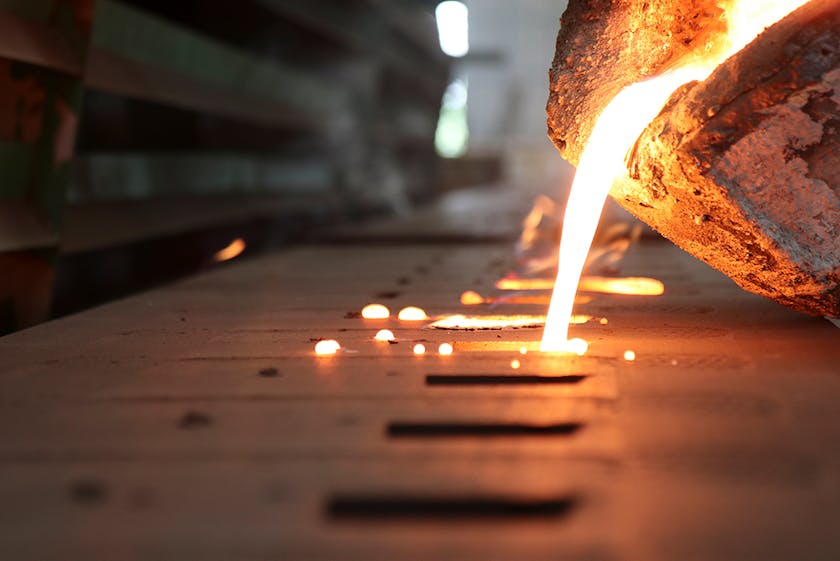
Investment Casting by MES Inc
Machining and Finishing Services
Casting companies offer additional services such as:
-
CNC machining
-
Vibratory tumble deburring
-
Precision hand deburring
-
Shot blasting
-
Thermal deburring
These services help achieve the final product specifications and reduce material waste. Casting service providers often offer value-added services that include various forms of expertise or training, making it crucial for clients to inquire about these offerings to ensure their specific needs are met.
Companies with integrated in-house machining capabilities and testing can streamline the production process and prevent conflicts if defects are found during machining. Casting companies that extend their services to include machining and finishing offer clients a completely manufactured and assembled product, demonstrating the importance of full-service casting providers in delivering end-to-end solutions.
5 HOW CASTING CREATES VALUE FOR CLIENTS
Casting services offer the following benefits:
-
Facilitate rapid prototyping, enabling clients to promptly iterate and refine their product designs prior to full-scale production
-
Use advanced casting techniques to achieve high-quality surface finishes and detailed reproduction of designs, giving clients a competitive advantage in their product offerings
-
Employ consistent and precision casting processes to ensure product reliability, which is crucial for client reputation and consumer trust.
Casting services provide the following benefits:
-
Cost savings through efficient material usage and reduced waste
-
Time savings by streamlining the production process
-
Scalability, ensuring clients can shift from prototyping to full-scale production without sacrificing quality
-
Meeting market demand and timelines
These benefits make casting services an essential resource for businesses.
Prototyping and Product Development
During the prototyping phase, casting plays a pivotal role in creating and testing product designs. The process includes:
-
CAD design
-
Prototype creation
-
Sample casting
-
Quality control
Prototyping with casting methods allows for quick design changes, reducing operational waste and verifying product reliability. This enables efficient design evaluation and concept exploration.
Casting companies offer precision prototyping capabilities for various materials, leveraging investment casting for high-precision components, crucial for parts with complex shapes or stringent tolerance demands. Scaling from prototypes to full production is made possible through the adjustability of casting tooling, catering to varying quantity needs and supporting business growth.
Scalability of Production
Casting services provide the flexibility to scale production based on client demand, from small batches to high-volume production runs.
Ensuring Quality and Consistency
Innovation within the casting industry significantly contributes to maintaining high standards of quality and consistency in the pieces produced. Employee development initiatives are integral in maintaining and enhancing the quality of casting services.
The adoption of new technologies is pivotal in fine-tuning the quality assurance process within the casting industry. Sustainable and environmentally friendly practices contribute to the overall framework of quality and consistency in casting services.
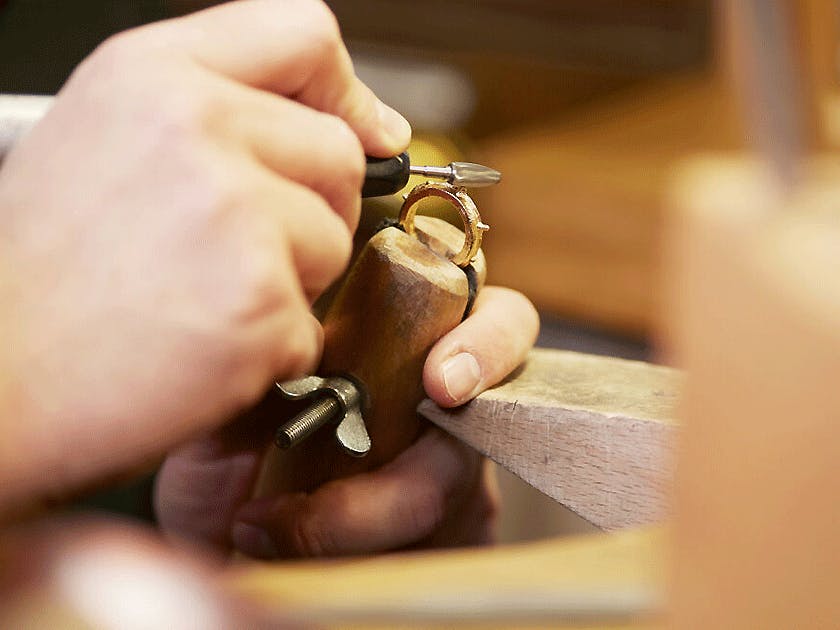
Chrome Diopside and Diamond Rings by Talisman Collection
6 CHOOSING THE RIGHT CASTING SERVICE PROVIDER
When selecting a casting service provider, consider the following factors:
-
Experience: Look for providers with experience in specialized markets like defense, nuclear, or aerospace, as they are valuable for meeting compliance and industry-specific requirements.
-
Capabilities: Choose suppliers that offer various casting processes to select the best option for specific component designs, applications, and sizes.
-
Certifications: Check if the provider has relevant certifications to ensure quality and compliance.
Providers who can meet requirements for both ferrous and non-ferrous alloys help to streamline vendor relationships. Evaluating service providers should be based on their product quality, service, and price to determine which aspect is most critical based on specific project needs.
Factors to Consider
Jewelry designers favor professional casting services due to their specialized knowledge and quality workmanship, especially when dealing with complex designs and diverse metals. Considering a casting service provider’s experience in specific markets is crucial for their ability to anticipate needs and address unique issues. It’s beneficial to select a casting provider that can furnish additional services, such as metallurgical expertise, design and material selection consultations, and training or information sharing, to enhance the overall metal expertise within a company.
Suppliers with integrated capabilities, such as in-house machining, can simplify the supply chain and reduce handling and shipping costs before the product reaches the customer.
Questions to Ask Potential Providers
When considering potential providers, there are a few key questions to ask:
-
Do they have experience with the specific materials or alloys your product requires?
-
Does the casting service provider’s company history and values resonate with your own?
-
Would you like to tour the casting service provider’s facility to gain a deeper understanding of their operational capabilities and company culture?
It’s also worth investigating whether the service provider can fulfill multiple product requirements to streamline your vendor relationships and reduce complexity. Lastly, look into the stability, history, and future prospects of the casting service provider to ensure they are a reliable and long-term business partner.
7 TAILORED SOLUTIONS FOR SPECIALIZED CASTING NEEDS
AFC Custom Engineered Components offers precision-tailored solutions for specific applications where standard fasteners fall short. They provide custom wire forms, castings, and injection-molded products that cater to unique project needs. The company elevates project outcomes with a strategic focus on material selection, extending an array of options including metals, plastics, composites, and specialized alloys suited to various performance and durability criteria.
AFC utilizes an assortment of manufacturing processes, including:
-
Precision machining
-
Injection molding
-
3D printing
-
Casting
Each process is deliberately chosen based on the complexity and specific property requirements of the components to provide tailored solutions.
Case Studies of Custom Casting Projects
Several case studies illustrate the versatility and innovative techniques used in custom casting projects. Plymouth Foundry produced specialized casts of C130 Gray Iron pipe for a global off-road equipment supplier, meeting stringent ISO 9001:2015 and PPAP standards by using green-sand molding.
A small-batch order of manifolds using Hi Si Mo Ductile Iron for off-road equipment was executed with high precision to adhere to strict material specifications.
In a blend of traditional craftsmanship and modern technology, 3D printed sand-cores streamlined the production of a complex custom impeller, eliminating the necessity for multiple conventional cores.
Innovation in Casting Techniques
Years of experience in the casting industry have a significant impact on the quality of work and fuel innovation in casting techniques. The benefits of experience include:
-
Accrued knowledge
-
Understanding of best practices
-
Ability to troubleshoot and problem solve
-
Familiarity with different materials and their properties
-
Knowledge of industry trends and advancements
The combination of accrued knowledge and the willingness to explore new techniques results in innovative solutions that fulfill unique production requirements.
The continuous drive for innovation ensures that casting techniques remain relevant, efficient, and adaptable to evolving market demands.
8 SUMMARY
In summary, jewelry casting is a blend of art and technical precision, shaping precious metals into intricate pieces of jewelry. Experienced casting specialists, with their wealth of knowledge and commitment to innovation, play a critical role in delivering high-quality products. Comprehensive casting services, from custom mold making to machining and finishing, cater to a diverse range of industries. Casting services offer significant value to clients through rapid prototyping, scalability of production, and ensuring quality and consistency. When choosing a casting service provider, it’s essential to consider factors such as experience, capabilities, certifications, and their ability to provide tailored solutions for specialized casting needs.